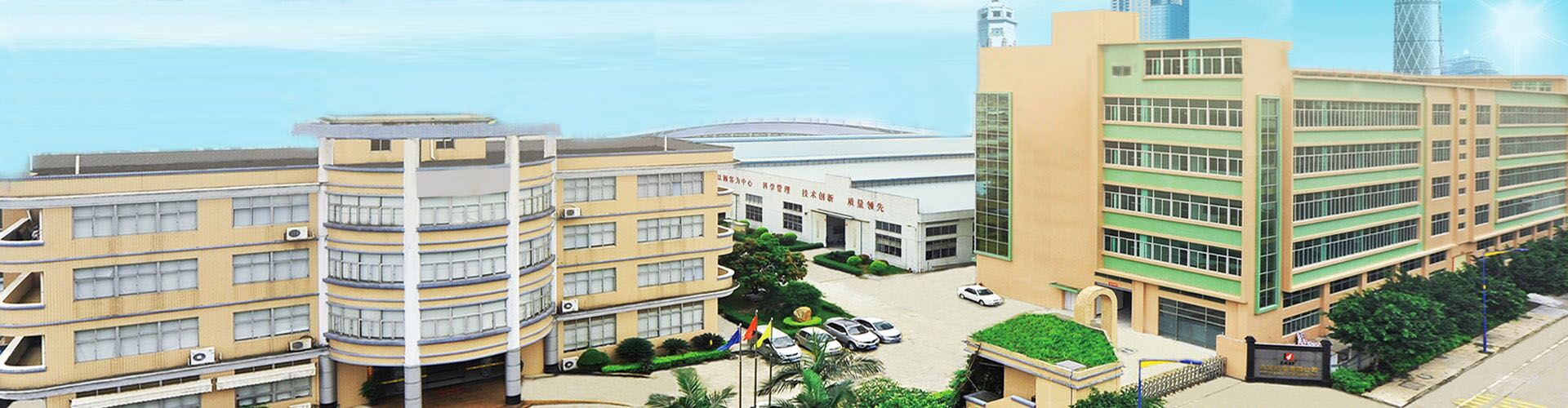
Join TMAX, become an agent!
Sales Manager:David
Email:David@tmaxcn.com
Wechat:18659217588
Item No.:
TMAX-XHPTPayment:
L/C, T/T, Western Union, Credit Cards, PaypalShipping port:
Xiamen PortLead Time:
5 DaysCertificate:
CE, IOS, ROHS, SGS, UL CertificateWarranty:
Two years limited warranty with lifetime technical support
Automatic Film Coating Coater Battery Electrode Slot Die Coating Machine
Machine main specifications
1.Base material basic parameters |
||
|
Cathode substrate |
Anode substrate |
Name |
copper foil |
aluminum foil |
thickness |
(8-30) μm |
(10-30) μm |
Width of substrate |
(200-320) mm |
(200-320) mm |
2.Coating parameters |
||
Material |
cathode film |
Anode film |
Graphite, mesophase carbon, hard carbon, etc |
Lithium cobalt acid, nickel cobalt manganese lithium, lithium manganese acid, lithium ferrous phosphate |
|
Dry coating thickness |
(50-150) μm (excluding single dry foil) |
(50-150) μm (excluding single dry foil) |
Wet coating thickness: |
100μm~300μm |
100μm~300μm |
solid content |
(40-70) ±5% |
(30-80) ±5% |
specific gravity |
(1.0-1.4) g/cm3 |
(1.0-2.5) g/cm3 |
viscosity |
(2500-8000) CPS |
(1000-10000) CPS |
temperature |
Control by process RT~140℃,adopt electric heating method |
|
solvent |
NMP Oil system/drainage system |
NMP Oil system/drainage system |
3.Basic machine parameters |
||
Width of coating roller |
400mm |
|
Effective coating width |
300mm and below |
|
Coating method |
Continuous extrusion coating (including strip coating) / intermittent extrusion coating |
|
Coating speed |
1~5m/min (Related to oven temperature, film state and coating process Settings); |
|
Power supply |
380 V x 50 Hz, three phase(ontrol power supply 220 V x 50 Hz, single phase) |
|
Total power |
Max. 50KW |
|
air source |
0.6 MPa |
|
Total machine length: not more than 10 meters |
Machine Structure
NO. |
Item |
Technical parameters |
1 |
Roller mounting structure |
Rack mounting method |
2 |
Roller surface treatment |
Metal aluminum roller surface oxidation |
3 |
Tension control system |
The closed loop automatically controls the constant tension, and the tension range is 0~50N |
4 |
Rectify way |
Automatic EPC control, stroke 80mm |
5 |
Winding way |
The roll is fixed by the 3-inch inflatable shaft; |
Unwinding single shaft support |
||
6 |
Direction of substrate operation |
Positive and reverse |
7 |
Substrate running speed |
5m/min |
8 |
Maximum rewinding diameter |
Ф300mm |
9 |
Maximum load bearing capacity of expansion shaft |
100Kg |
10 |
The number of inflating shaft strips in winding |
1 |
11 |
Main drive motor |
Servo motor + precision planetary reducer |
12 |
toolsetting |
Servo + keenes grating ruler |
13 |
Roller surface treatment |
Surface oxidation of metal aluminum roller, circular jump ≤30um |
14 |
Coating type |
Continuous extrusion coating/gap extrusion coating |
15 |
Die parameters |
Die width: at 20 ℃, die length is 400mm ± 0.5mm; Body material: 15-5PH stainless steel; Channel surface polishing accuracy: 4-6ra (micro inch); Feeding position: back feeding; Products and applications: 3-300 μ m positive / negative paste, lithium-ion battery application |
16 |
Coating roll (steel roll) |
Special steel pipe, diameter Φ 120mm, hard chrome plating Circular run out accuracy within 2um Linear speed range 2-5M / min There is no abnormal noise, vibration and heat in each part during driving rotation |
17 |
Roller specification |
Diameter Ø80mm, surface imported EPDM rubber |
18 |
Slot die head movement |
Base drive: push button operation (use a cylinder to move a wide range) Clearance adjustment: button operation (actuated by servo motor) Gap detection: grating ruler (accuracy 1um) |
19 |
Single head position |
Installation and operation before drying |
1. Integral rewinding, coating head mechanism
NO. |
Name |
Description |
1 |
Screw pump |
Japanese Soldier Screw Pump |
2 |
Transit pot |
Volume 30 L, pressure control, liquid level detection, slow stirring |
3 |
Material backflow coating controller |
Material backflow coating controller |
4 |
Filter |
customized according to customer requirements |
5 |
De-ironing separator |
Above 8000 gauss |
6 |
Pressure balance buffer |
Make sure the pressure in the pipeline is balanced |
7 |
Pipelines and accessories |
Stainless steel quick joints and stainless steel pipe fittings |
8 |
Pressure monitoring system |
Each part of the pipeline is monitored by a pressure monitoring system |
2.Pumping system
NO. |
Name |
Description |
1 |
Screw pump |
Japanese Soldier Screw Pump |
2 |
Transit pot |
Volume 30 L, pressure control, liquid level detection, slow stirring |
3 |
Material backflow coating controller |
Material backflow coating controller |
4 |
Filter |
customized according to customer requirements |
5 |
De-ironing separator |
Above 8000 gauss |
6 |
Pressure balance buffer |
Make sure the pressure in the pipeline is balanced |
7 |
Pipelines and accessories |
Stainless steel quick joints and stainless steel pipe fittings |
8 |
Pressure monitoring system |
Each part of the pipeline is monitored by a pressure monitoring system |
3.Oven
No. |
Item |
Technical parameters |
1 |
Oven structure |
Double heating, up and down |
2 |
Oven length |
6m (2 m/section*3) |
3 |
Texture |
SUS304 stainless steel, inner liner 1.0mm, outer liner 1.2mm |
4 |
Oven guide roller drive mode |
Passive idler drive |
5 |
temperature control |
Divided into normal working temperature control, over temperature monitoring and alarm protection control, cut off heating power when over temperature; each section is completely independent control |
6 |
Heating Mode |
Electric heating, hot air circulation structure |
7 |
Single section oven heating power |
12KW/2m |
8 |
Internal temperature of drying channel |
Designed Max150℃, temperature difference in single section oven ≤5℃ |
9 |
Box surface temperature during operation |
≤45℃ |
10 |
Blowing way |
The upper and lower air blowers, the up and down air volume are controlled by valves respectively; the upper and lower air chambers share the heating body |
11 |
Exhaust volume control for each section |
Circulating fan air volume 3000m³ / h (single section) Exhaust air volume 4000m³ / h |
12 |
Structure of the wind |
The blowing direction is 30 degrees from the horizontal. The air nozzle slot is slotted with a special mold. |
13 |
Heating control |
solid-state relay |
14 |
Fan material |
SUS304 stainless steel |
15 |
Solvent recovery system |
NO just help install the interface |
16 |
NMP solvent concentration alarm |
NO |
17 |
Wind chamber pressure monitoring |
NO |
4. Winding mechanism: the function is the same as that of unwinding, which is added as follows
NO. |
Item |
Technical parameters |
1 |
tension |
One set is installed in front of the traction roller, and the constant tension is automatically controlled. The tension range is 0 ~ 50N. |
2 |
Installation structure |
Square frame welding base frame, one side vertical plate |
3 |
Number of inflating axis in winding |
1(one-armed winding) |
4 |
Winding roll diameter |
Ф300mm |
5 |
Winding rectification |
Automatic EPC control, stroke 80mm |
5.Control system
NO. |
Item |
Technical parameters |
1 |
Master control system |
ouch screen, PLC, module, servo system |
2 |
mode of operation |
Manual, automatic, emergency stop; |
3 |
Coating, intermittent length set range |
Coated length 20.0~3200.0mm Intermittent length 5.0~3200.0mm |
4 |
Alarm condition |
In case of equipment failure, the touch screen will display the corresponding correction screen |
5 |
Count function |
Production quantity/length |
1 Standard exported package: Internal anticollision protection, external export wooden box packaging.
2 Shipping by express, by air, by sea according to customers' requirements to find the most suitable way.
3 Responsible for the damage during the shipping process, will change the damage part for you for free.
Previous :
Automatic Roll To Roll Coating Machine For Battery Electrode ProductionNext :
Integral Dry Room For Li-Polymer Battery ManufacturingCategories
© Copyright: 2025 Xiamen Tmax Battery Equipments Limited All Rights Reserved.
IPv6 network supported