Xiamen Tmax Battery Equipments Limited was set up as a manufacturer in 1995, dealing with Laboratory equipments, technology, etc. We have total manufacturing facilities of around 2, 000 square meters and more than 100 staff. Owning a group of experie-nced engineers and staffs, we can bring you not only reliable products and technology, but also excellent services and real value you will expect and enjoy.
Perovskite solar cells (PSCs) represent a promising photovoltaic technology due to their high efficiency, low manufacturing costs, and versatility. These devices are based on lightabsorbing perovskite materials, typically hybrid organicinorganic lead or tin halidebased materials with a perovskite crystal structure. Below is an overview of the key components and steps involved in the fabrication of a perovskite solar cell device:
Key Components of Perovskite Solar Cell Devices
1. Transparent Conductive Oxide (TCO) Layer
Usually made from materials like fluorinedoped tin oxide (FTO) or indium tin oxide (ITO), this layer serves as the front contact and allows light to enter the cell while conducting the generated electrical current.
2. Electron Transport Layer (ETL)
Positioned between the TCO and the perovskite layer, the ETL facilitates the extraction of electrons from the perovskite material towards the TCO. Common materials include titanium dioxide (TiO₂), tin dioxide (SnO₂), and fullerene derivatives (e.g., PCBM).
3. Perovskite Light Absorber Layer
The heart of the PSC, this layer absorbs sunlight and converts it into electrical charges. The most commonly used perovskite composition is methylammonium lead iodide (MAPbI₃), though other compositions such as formamidinium lead iodide (FAPbI₃) and cesiumdoped perovskites are also popular for their improved stability and efficiency.
4. Hole Transport Layer (HTL)
This layer collects holes (positive charges) from the perovskite material and transports them towards the back contact. SpiroOMeTAD is one of the most widely used HTL materials, although alternatives like poly(triarylamine) (PTAA) and copper(I) thiocyanate (CuSCN) are also explored for costeffectiveness and improved performance.
5. Back Contact/Electrode
Typically made from metals like gold, silver, or aluminum, the back contact collects the charge carriers transported through the HTL and completes the electrical circuit.
Slot Die Coater
Fabrication Process
1. Substrate Preparation
Clean the transparent conductive oxidecoated substrate (such as FTO or ITO coated glass) thoroughly to remove any contaminants.
2. Deposition of Electron Transport Layer
Deposit the ETL onto the cleaned substrate using techniques such as spin coating, spray pyrolysis, or sputtering.
3. Formation of Perovskite Layer
Apply the perovskite material onto the ETL using methods like spin coating, slotdie coating, or vapor deposition. Postdeposition annealing is often required to improve crystallinity and enhance device performance.
4. Application of Hole Transport Layer
Deposit the HTL over the perovskite layer, typically via spin coating or thermal evaporation.
5. Back Electrode Deposition
Finally, deposit the back electrode, usually by thermal evaporation or sputtering, completing the device architecture.
6. Encapsulation
To protect the device from environmental factors like moisture and oxygen that can degrade the perovskite material, encapsulation is crucial. This step involves sealing the device within a protective barrier, which could be a laminate or a glass cover with adhesive.
Performance and Challenges
Efficiency: Perovskite solar cells have demonstrated efficiencies exceeding 25%, making them highly competitive with traditional siliconbased solar cells.
Stability: One of the main challenges facing PSCs is their longterm stability under operational conditions. Research focuses on improving the intrinsic stability of perovskite materials and developing effective encapsulation strategies.
Scalability: While laboratoryscale production has achieved impressive results, scaling up these processes to commercial levels presents additional challenges related to uniformity, defect density, and cost.
By addressing these challenges, perovskite solar cell technology holds great promise for future photovoltaic applications, potentially revolutionizing the renewable energy landscape with its unique combination of high efficiency, low cost, and flexibility.
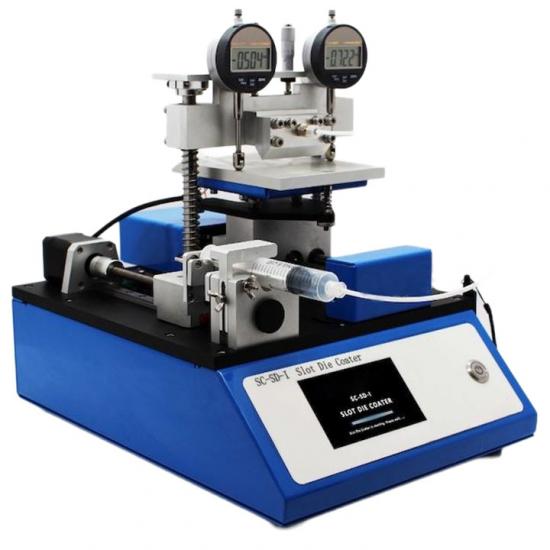